Assembly GAS BOX for the Medical Industry
Project Description:
The stainless steel enclosure, with its sweeping arcs and spherical shape, is custom-crafted for the medical industry, showcasing our expertise. Our welding and forming techniques are highly complex, demanding strict adherence to standards to ensure uniform aesthetics and cleanliness of both inner and outer surfaces. We also maintain rigorous requirements for welding seam integrity.
Processes:
-
Laser Cutting
-
Thread Tapping
-
Deburring
-
Stud & Nut Staking
-
CNC Bending
-
CNC Machining
-
Welding
-
Polishing
-
Assembly
-
Packaging
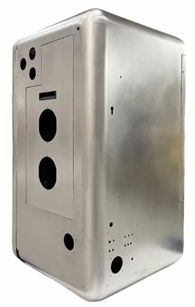
DFM Involvement from the Design Phase
-
Material Localization: We collaborate with clients to substitute British standard materials with locally sourced equivalents, ensuring functional performance and adherence to specified dimensions.
-
Tooling Design Cost Saving: Utilizing existing spherical tooling sizes and innovative welding techniques, we achieve substantial cost savings and expedite New Product Introduction (NPI) timelines, addressing clients' cost considerations effectively.
-
Weld Fixture Optimization: Using a 3D flexible welding table and our seasoned welding processes, we reduce welding deformations, ensuring consistent quality and meeting stringent tolerance criteria, leading to significant cost reductions for our clients.

3D flexible welding table and fixture
FMEA Assessment:
-
Precision in Bending Process: We develop advanced inspection gauges to ensure consistent alignment between cabinets and doors, reflecting our commitment to precision.
-
Uniform Appearance Control: We establish meticulous work instructions and optimize the polishing process flow from project initiation, minimizing the risk of polishing inconsistencies and ensuring a uniform, aesthetically pleasing finish.
-
Cleaning and Packaging Excellence: We prioritize cleanliness and safety by using an ultrasonic cleaning process and packaging products in a class 10,000 clean room, ensuring that our clients receive reliable and immaculate products.
Control Plan - Mass Production:
For critical processes such as welding, polishing, and cleaning, we implement stringent process controls. Detailed work instructions and inspection checklists are meticulously developed for each stage to guarantee the production of high-quality, dependable products with consistent results. Our dedication to exceptional problem-solving capabilities, risk assessment, and customer-centric processing underscores our commitment to quality excellence and customer satisfaction.