Assembly Enclosures for the Energy Storage Industry
Project Description:
We developed the DCFC (Direct Carbon Fuel Cell) Assembly Enclosure for the Energy Storage industry, which demanded the highest standards in precision, welding reliability, and explosion-proof requirements. We are proud of our NPI team's performance as we completed the project within two weeks and achieved mass production of 10,000 units within six weeks. This has helped our client swiftly and efficiently meet the market's requirements.
Processes:
-
Laser Cutting
-
Stamping
-
Thread Tapping
-
Deburring
-
Stud & Nut Staking
-
CNC Bending
-
Welding
-
Powder Coating
-
Assembly
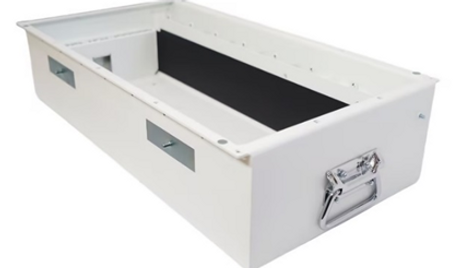
DFM Involvement From The Design Phase:
-
Material Localization: Strategically sourcing and materials localization optimize costs and lead times, ensuring timely project completion without compromising quality.
-
Tooling Design Cost Saving: Utilize existing tooling and innovative design approaches to streamline production, resulting in significant cost savings and expedited New Product Introduction (NPI) schedules.
-
Plating Cost Reduction: Optimize product structure to improve zinc plating quality and reduce costs, ensuring durability and longevity of the final product.
-
Mass Productivity Improvement: Engage our automation team early in the design phase to introduce advanced bending and welding robots, enhancing mass production stability and improve productivity by up to 40%.

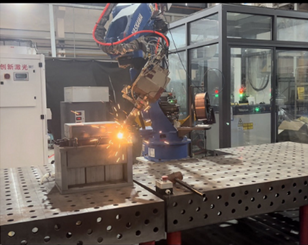
Bending & Welding Robot implementing
FMEA Assessment:
-
Bending Process Precision: Rigorously assess critical dimensions based on customer functional requirements, supported by the development of inspection gauges to ensure consistent bending precision and quality
-
Welding Strength Reliability: Develop welding coupons and conduct thorough strength testing to ensure the reliability of welds. Refine welding methods and parameters to consistently deliver top-quality results.
-
Powder Coating Optimization: Utilize Design of Experiments (DOE) experiments to identify optimal oven settings for powder coating, ensuring uniformity and quality across materials of varying thicknesses. 100% testing thickness, adhesion, color difference for every batch, guarantees robust quality assurance.


Bending Inspection Gauges

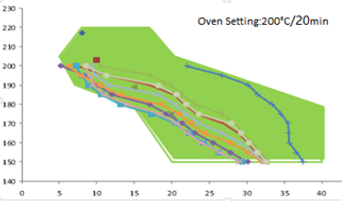
DOE process to check the best oven setting
Control Plan - Mass Production:
Integrate critical parameters, checkpoints, fixtures, and inspection jigs into a quality control Checklist of our Manufacturing Execution System (MES). Ensure compliance with the highest quality standards for products and seamless execution of mass production processes.